Keys to successful project management. Successful completion of a construction project means achieving the project objectives within the defined scope of the bid, budget and schedule.
We must also ensure that the quality of the work complies with established standards and that all necessary requirements and regulations are followed throughout the construction process.
As mentioned in previous publications, in order for this to happen, the project or work must come from a reliable technical and economical proposal.
Successful Projects: Tips for Project Management
Strategies for Achieving Your Goals. Through these strategies, project managers can ensure that their projects are completed on time and on budget.
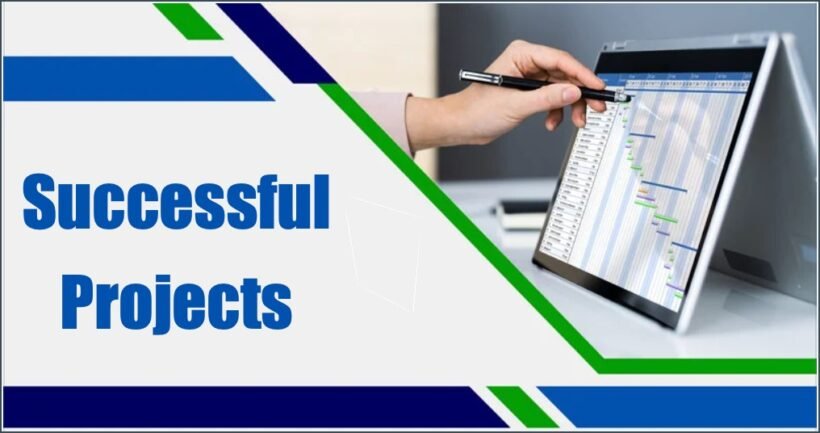
The main strategies to follow for achieving a project’s success are analyzed below:
Prefabricated, skid-mounted, and modular design
Prefabricated, skid-mounted, and modular design in construction and assembly works
Prefabricated, skid-mounted design, and modular design is construction methods that involve the use of pre-made components or modules to construct.
These methods offer several advantages over traditional construction techniques, including increased efficiency, reduced construction time, cost-effectiveness, and improved quality control.
1. Prefabricated Design:
Prefabrication means the process of manufacturing off-site building components, pipe spools or electrical system components in a plant-controlled environment.
These components are then quickly transported and assembled on site.
Prefabricated design has the following key features:.
- Efficiency: Prefabricated elements are produced in a controlled environment with specialized machinery, which allows for efficient and precise manufacturing.
- Time-saving: Since many components are manufactured simultaneously and can be installed quickly on-site, the construction process is significantly faster compared to traditional methods.
- Quality control: Factory-based production ensures consistent quality, as it minimizes the impact of adverse weather conditions and on-site variables.
- Reduced waste: Material waste is minimized since components are made to precise measurements, reducing the need for excess materials.
2. Skid Design:
Skid design, also known as skid-mounted design or modular skid design, refers to a specific method of prefabrication where various equipment and components are mounted on a single structural steel frame or base, known as a "skid."
These skids are then transported to the site as self-contained units and can be easily installed or integrated into larger industrial systems or processes.
Skid design is commonly used in industries such as oil and gas, petrochemicals, power generation, and water treatment, among others. The key features of skid design include:
- Compact and self-contained: Skids are preassembled units that include equipment, instruments, and other necessary components, all mounted on a single base. This makes them easy to transport and install.
- Interchangeability: Skids can be designed for specific purposes or processes, and they can be easily interchanged or replaced, offering flexibility and adaptability.
- Quality control: The manufacturing of skids takes place in a controlled environment, ensuring consistent quality and reducing on-site construction risks.
- Faster installation: Since skids are preassembled, the installation process is faster, leading to reduced downtime during on-site implementation
Modular design:
Modular design takes prefabrication a step further by creating complete modules or units that can be combined or stacked to create a variety of structures.
These modules are usually self-sufficient and can be designed to work independently or as part of a larger system. Key features of the modular design include:
Flexibility: Modular buildings can be easily expanded, modified, or taken apart, making them ideal for situations where adaptability is essential.
Scalability: The build can be easily scaled up or down by adding or removing modules, making it suitable for a wide range of projects.
Mobility: Some modular structures are designed to be mobile, allowing them to be relocated if necessary.
• Applicability – The modular design is well suited to various types of buildings, including residential, commercial, educational, and healthcare facilities.
Recruit skilled workers for the construction / assembly industry
Hire skilled workers in the construction and assembly industry
Recruit skilled workers are crucial for the successful completion of projects and ensuring high-quality work.
Steps and strategies to help you attract and hire skilled workers:
1. Define the requirements of the position: Clearly describe the competencies, qualifications and experience you are seeking from potential candidates. This will help you focus on the right people and simplify the hiring process.
2. Post job openings on popular job websites and construction-specific platforms by using online job platforms. Web sites such as Indeed, LinkedIn and sector-specific job boards can reach a broad audience of potential applicants.
3. Connect with local trade schools, technical colleges, and vocational training centers that offer related programs in your industry.
4. Participate in construction job fairs and industry-related events to meet potential candidates in person.
5. To attract skilled workers, it is important to offer competitive salaries and benefits. Ensure that your salary and benefits packages are competitive within the industry to attract top talent.
6. Provide Skills Development Opportunities: Highlight opportunities for skills development and career progression within your organization. Skilled workers are more likely to join companies that invest in their professional development.
7. Showcase your company's projects and culture on your company's website and social media platforms to showcase completed projects, testimonials from satisfied clients, and a positive work environment. Skilled workers can be attracted by a strong company reputation.
8. Encourage your current skilled workers to refer potential candidates to your company through Employee Referral Programs. Employee referrals often result in high-quality hires that fit well within the company culture.
9. During the hiring process, conduct in-depth skills interviews and assessments to assess candidates' technical abilities and their compatibility with your team.
10. Offer competitive advantages: Consider offering additional benefits such overtime, health and wellness benefits, paid time off or bonuses. These incentives can help your company stand out from your competitors.
11. Skilled workers prioritize safety in their work environment. Recognize your company's commitment to maintaining a safe workplace and respecting security regulations.
It's important to remember that finding skilled workers is not just about finding individuals with technical expertise, but also those who align with your company's values and culture. A strong and skilled workforce will contribute to the long-term success of your projects.
Optimizing Material Management
Improving material management
To ensure cost-effectiveness, reduce waste, and improve overall project efficiency, it is crucial to optimize material management in construction and assembly projects. These strategies can help you achieve effective material management:
1. To ensure accuracy in project planning, it is important to plan the project thoroughly, including estimating the required materials based on documentation and technical specification engineering.
2. Maintain strict quality control measures to ensure that the materials meet the required technical specifications.
3. Establish a centralized procurement system to coordinate material orders. By doing this, you can buy in bulk, negotiate better prices, and minimize the risk of duplicate or unnecessary orders.
4. To ensure high-quality materials are delivered on time, it's important to work with reliable and reputable vendors. Regularly assess vendor performance to ensure they meet your project requirements and deadlines.
5. Ensure that a robust material tracking system is implemented to monitor the movement of materials from procurement to usage for Material Tracking and Inventory Management. To prevent shortages or overstocking, it is important to regularly update and reconcile inventory levels.
6. When possible, use a just-in-time delivery approach, which means that materials are delivered to the construction site exactly when they are needed. This minimizes the need for on-site storage and reduces the risk of theft or damage.
7. To reduce material wastage during construction, develop a waste management plan. Reuse or recycle materials whenever possible, and follow practices that reduce on-site losses.
8. Material handling equipment: Use appropriate material handling equipment, such as cranes, forklifts, or conveyors, to efficiently transport materials to the site and reduce the risk of damage.
9. Training and Communication: Provide training to construction personnel on proper material handling, storage, and use. Effective communication ensures that everyone comprehends the significance of material management and its impact on the project's success.
10. Regular audits and reviews: Perform regular audits of equipment utilization, inventory levels and procurement processes. Examine the data to identify areas for improvement and take corrective measures.
11. Technology Integration: Adopt construction management software and technology solutions that offer real-time hardware tracking, automated inventory management and data analysis. These tools have the potential to enhance transparency and effectiveness.
12. Contingency Planning: Account for potential delays or changes in material availability during project planning. Make sure to have backup suppliers or materials in place to prevent any disruptions to the construction timeline.
Prioritize Safety in construction / assembly projects
Make safety a priority in construction and assembly projects
Safety is of paramount importance in construction projects to protect workers, visitors, and the general public from potential hazards. Implementing comprehensive safety measures can significantly reduce accidents and injuries. Here are some essential steps for ensuring safety in construction projects:
1. Develop a Safety Plan: Prioritize safety right from the project's planning phase. Create a comprehensive safety plan that outlines the safety procedures, identifies potential hazards, and establishes safety protocols for different tasks.
2. Training and Education: Ensure that all construction personnel, including workers, supervisors, and contractors, receive proper safety training. This training should cover potential hazards, safe work practices, proper use of personal protective equipment (PPE), emergency procedures, and more.
3. Provide Personal Protective Equipment (PPE): Supply and enforce the use of appropriate PPE for all workers and visitors on the construction site. Common PPE includes hard hats, safety goggles, gloves, ear protection, and steel-toed boots.
4. Regular Inspections: Conduct regular safety inspections of the construction site to identify potential hazards or unsafe practices. Address any issues promptly to prevent accidents.
5. Hazard Identification: Regularly assess the site for potential hazards, including those related to falls, electrical work, heavy machinery, and hazardous materials. Take steps to eliminate or mitigate these risks.
6. Implement Safety Signage: Place clear and visible safety signs throughout the construction site, indicating potential dangers, required PPE, emergency exits, and more.
7. Controlled Access: Limit access to the construction site to authorized personnel only. Install barriers or fences around the site to prevent unauthorized entry.
8. Scaffolding and Fall Protection: Ensure proper installation and maintenance of scaffolding, guardrails, and fall protection systems to prevent falls from elevated areas.
9. Machinery and Equipment Safety: Train operators in the safe operation of machinery and equipment. Regularly inspect and maintain equipment to keep them in proper working condition.
10. Emergency Preparedness: Develop and communicate emergency response plans to handle accidents, injuries, fires, or other emergencies effectively. Conduct regular drills to familiarize personnel with the procedures.
11. Regular Safety Meetings: Hold regular safety meetings to discuss safety concerns, share best practices, and address any new or emerging hazards on the site.
12. Subcontractor Safety: Ensure that all subcontractors working on the project adhere to the same safety standards as the primary contractor.
13. Incident Reporting and Investigation: Establish a clear procedure for reporting incidents and near-misses. Investigate accidents to identify the root causes and implement measures to prevent similar incidents in the future.
14. Safety Incentives: Consider implementing safety incentive programs to encourage workers to prioritize safety and maintain a safe working environment.
15. Stay Compliant with Regulations: Stay updated with local, state, and federal safety regulations and ensure compliance with all applicable laws.
Remember, safety is an ongoing process that requires the commitment of everyone involved in the construction project. By prioritizing safety and consistently following these steps, construction companies can significantly reduce the risk of accidents and create a safer work environment.
Quality Control
The importance of quality control in successful projects
Quality control is a systematic process that ensures the construction or assembly project meets the required quality standards. The importance of quality control in construction is highlighted in these key aspects:
1. Define clear and specific quality standards for different aspects of the construction project, including materials, workmanship, safety, and functionality. These standards should align with industry best practices, relevant regulations, and client specifications.
2. Quality Planning: Develop a quality control plan that describes the procedures and processes required to achieve the defined quality standards. All phases of the project, including design, procurement, construction, and final inspection, should be covered by the plan.
3. Conduct regular inspections at various stages of the construction process to ensure that the work meets the established quality standards. Inspections can be carried out by quality control personnel or by independent inspectors.
4. Keep detailed records of all quality control activities, including inspection reports, test results, and corrective actions taken. Traceability and a historical record of the project's quality performance are made possible by proper documentation.
5. Material testing: Only use materials that meet or exceed the technical specifications of the project. Request that each material's quality certificate indicate and comply with the current Standards.
6. Monitor the execution of construction activities to ensure they are performed correctly and meet required standards. Appropriate training and supervision of workers is essential to maintaining high quality performance.
7. Corrective action: When deviations from quality standards are found, take corrective action quickly and effectively. Preventing compounding problems and potential rework can lead to cost and time savings by addressing issues early.
8. Quality Checks: Conduct periodic quality checks to evaluate the overall effectiveness of quality control measures. Systemic issues and areas for improvement can be identified through audits.
9. Ensure that the construction project complies with building codes, safety regulations, and environmental standards. The construction process must prioritize safety as an integral part of quality control.
10. Continuous Improvement: Focus on a culture of continuous improvement across the construction team. Ensure that quality control procedures are regularly reviewed and updated based on lessons learned and project requirements.
11. To enhance the skills and knowledge of your personnel, invest in training programs. Qualified and well-trained workers are more likely to provide quality work.
Quality control is a continuous process that requires the commitment and cooperation of all stakeholders involved in the construction project.
Invest in Technology
Winning Projects: Investing in Technology
Investing in technology for a successful construction project can provide numerous benefits, ranging from increased efficiency and productivity to improved safety and project outcomes. Here are some key areas where technology can make a significant impact:
1. Construction Management Software: Utilize construction management software to streamline project planning, scheduling, and communication. These platforms centralize project data, facilitate collaboration among team members, and offer real-time updates on progress, issues, and changes.
2. Building Information Modeling (BIM): Implement BIM technology for 3D modeling, visualization, and coordination. BIM enables better design collaboration, clash detection, and helps identify and resolve potential conflicts early in the project, leading to cost savings and reduced rework.
3. Mobile Apps and Cloud Solutions: Equip on-site teams with mobile apps that provide access to project documentation, drawings, and communication tools. Cloud-based storage allows easy sharing and synchronization of project data, enhancing communication and efficiency.
4. IoT and Sensors: Use Internet of Things (IoT) devices and sensors to monitor equipment, machinery, and construction site conditions. It enables real-time data collection, predictive maintenance, and improved safety monitoring.
5. Drones: Deploy drones for aerial surveys, site inspections, and progress monitoring. Drones can quickly capture high-resolution images and videos, providing a comprehensive view of the project site and aiding in decision-making.
6. Augmented Reality (AR) and Virtual Reality (VR): Utilize AR and VR for enhanced project visualization and stakeholder engagement. These technologies allow clients and stakeholders to experience the project in an immersive way, leading to better understanding and feedback.
7. Robotics and Automation: Explore robotics and automation for repetitive construction tasks, such as bricklaying, welding, and material handling. Robots can improve speed, precision, and safety in these activities.
8. Artificial Intelligence (AI) and Data Analytics: Harness AI and data analytics for project insights, risk analysis, and performance optimization. AI can process vast amounts of data to identify patterns, predict potential issues, and support data-driven decision-making.
9. Safety Technology: Adopt safety-focused technology, such as wearable devices for workers, smart helmets, and proximity sensors. These technologies enhance on-site safety by monitoring conditions and alerting workers to potential hazards.
10. Document Management Systems: Utilize document management systems to organize and control project documentation, ensuring the latest revisions are accessible to all stakeholders.
11. Collaborative Communication Tools: Integrate communication tools that facilitate collaboration, such as instant messaging platforms, video conferencing, and virtual meeting rooms.
Staying updated with the latest advancements in construction technology ensures that the project remains competitive and efficient in a rapidly evolving industry.
Budget and Financial Management
Successful project management involves budgeting and financial management
Budget and financial management are critical components of a successful construction project.
Effective financial planning and control help ensure that the project stays on track, meets financial goals, and is completed within the allocated budget.
Here are key considerations for budget and financial management in a successful project:
1. Detailed Cost Estimation: Begin with a comprehensive, cost estimate during the project planning phase.
Consider all direct and indirect costs, including labor, materials, equipment, subcontractors, permits, and contingencies.
2. Establish a Realistic Budget: Based on the cost estimation, set a realistic and well-defined budget for the entire project.
The budget should align with the project's scope and objectives.
3. Monitor Cash Flow: Monitor the project's cash flow regularly to ensure that funds are available when needed to cover expenses.
Proper cash flow management prevents delays and disruptions due to financial constraints.
4. Contingency Planning: Include contingency funds in the budget to account for unexpected events or changes that may arise during the construction process.
A contingency reserve helps mitigate risks and potential cost overruns.
5. Financial Tracking and Reporting: Implement a robust financial tracking system that provides accurate and up-to-date information on project expenditures, commitments, and budget variances.
Regular financial reports help in making informed decisions and taking corrective actions if needed.
6. Vendor and Subcontractor Management: Negotiate fair and competitive contracts with vendors and subcontractors.
Monitor their performance to ensure they deliver quality work within the agreed-upon costs.
8. Earned Value Management (EVM): Use Earned Value Management techniques to assess the project's performance against the budget and schedule.
EVM helps predict future cost and schedule trends, enabling proactive management.
9. Financial Risk Management: Identify potential financial risks, such as inflation, market fluctuations, and currency exchange rate changes. Develop strategies to mitigate these risks and protect the project's financial health.
11. Contract Management: Ensure compliance with contract terms and conditions. Monitor contract deliverables and payments to avoid disputes and delays.
12. Regular Financial, Reviews: Conduct regular financial reviews with the project team and stakeholders to keep everyone informed about the project's financial status and address any concerns proactively.
13. Auditing and Compliance: Perform periodic audits to verify financial records and compliance with relevant regulations and accounting standards.
14. Cost Control Measures: Implement cost control measures throughout the project's lifecycle, focusing on efficient resource allocation and reducing wastage.
15. Lessons Learned: Conduct a post-project financial review to analyze budget performance and identify areas for improvement in future projects.
The optimal profile required for the estimators group
Experienced personnel are needed for the estimator group
Estimation is a critical aspect of project management, and having experienced individuals in the team make a significant difference in the accuracy and reliability of estimates.
Experienced personnel who have the ability to define the logical sequence of execution for each stage of construction.
Request advice from specialists
When a project is complex, it's wise and prudent to seek specialized advice.
Complicated projects often have unique challenges, unusual technical requirements, and high stakes.
By seeking specialized expertise, your project's chances of success increase significantly.
Have accurate information on labour performance
It is essential to have accurate historical information on job performance to evaluate each of the project tasks.
In the next post, we will explore how to make Piping material Take Off
Keys to Successful Projects Management – Calculate Man Hours